|
|
|
News |
|
|
|
|
|
|
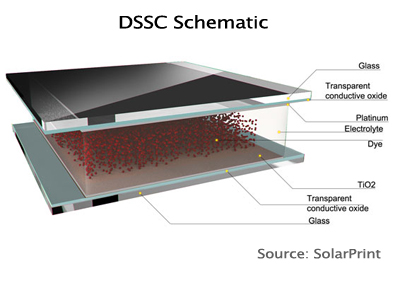 |
|
|
DSSC INTRODUCTION
Abstract
Dye-sensitized solar cells are the most cost-effective, third-generation solar technology available today. DSSC technology, invented in 1991 by Michael Gratzel and Brian O’Regan, has recently attracted more interest because of its low material cost, ease of production, and high conversion efficiency compared to other thin-film solar cell technologies. Nonetheless, due to technical constraints, the maximum efficiency is only half the efficiency of crystalline silicon-based solar cells. In an effort to replace the solar technologies we currently use, improving the efficiency of DSSC technology is critical for widespread adoption. The process parameters have a significant impact on determining the efficiency of the solar cell, as well as, the materials being applied. This paper will attempt to summarize the influence of material selection, the sintering process, and belt furnace parameters on the efficiency of dye-sensitized solar cells.
Introduction
Sintering of the electrode layer (composed of TiO2 and TCO) is an essential step when determining the overall efficiency of the solar cell. The process consists of a two stage sintering procedure where sintering of the layer occurs before and after dye implementation. Important parameters to note are the growth temperature, soaking time, and the heat rate; all of which will directly affect the outcome on the efficiency of the solar cell. Additionally, the materials selected for each segment of the cell will have an integral effect on the final efficiency as well. This paper will explore the ideal sintering process parameters and the material selections, as well as, the impact they both play on the overall efficiency of the solar cell.
Description
A dye-sensitized solar cell is composed primarily of three parts (as shown in figure 1). The first part, the substrate, is the negative terminal. The substrate has a layer of transparent glass on the outside and a coating of transparent conductive oxide (TCO) on the inside. This warrants sunlight to pass through. In the center sector, a layer of dye sensitizers bind to a layer of nano-structured titanium dioxide (TiO2), where the TiO2 is connected to the negative terminal to collect sunlight. All of the layers are then immersed in an electrolyte solution to allow charge transportation. The top part is the positive terminal and it contains a coating of carbon (graphite) or platinum for the purpose of transferring electrons. The outside layer is made of transparent glass and the top and bottom divisions are joined together to prevent the centered portion from leaking.
Electricity Generation Schematics
Initially, sunlight passes through the transparent conductive oxide (TCO) layer into the dye-sensitized layer exciting the electrons within the molecules. The electrons are then injected into the TiO2 particles (which act as a semiconductor) transporting light induced electrons toward the negative terminal. The negative terminal layer, or the TCO layer, is where all of the electrons are collected and then transported to the external circuit, generating electricity. Subsequently, the electrons are reintroduced into the solar cell through the positive terminal into the electrolyte. From here, the electrolyte transports the electrons back into the dye molecules and the process is repeated.
Materials Selection
The transparent coating for the negative terminal is made of a thin layer of fluorine-doped tin oxide. It is a substrate that enables sunlight to pass through it, conducting electricity.
For the semiconductor, either zinc oxide (ZnO) or titanium dioxide (TiO2) can be applied. TiO2 is the preferred choice and it is used most often because the surface is highly resistant to continuous electron transfer. Titanium dioxide, however, is not sensitive to visible light and it will only absorb a small amount of solar photons. Therefore, dye sensitizers have to be joined together with the titanium dioxide layer in order to harvest large portions of the sun’s light. Zinc oxide has higher electron mobility than titanium dioxide, however, it has a limited selection of organic dyes. This makes it a less suitable option until more exceptional alternative sensitizers are identified.
Dye-sensitizers can contain several classifications of materials. One option, the natural dye, can come from a variety of resources such as blue berries, blackberries, and raspberries. They are the easiest to come by and are excellent for student training courses and/or for testing purposes. A second option, the synthetic dye, provides better performance because of its optimized light collection property.
The material used for the positive terminal layer, or the cathode layer, can be platinum or carbon (graphite). Platinum is more efficient, however, the carbon alternative is the easiest and least expensive to use (great for school work or testing purposes).
Advantages
The advantages of DSSC compared to alternative options for solar electrical generation, is that DSSC has a high price/performance ratio. This means that it is less expensive to assemble, as well as, light and mechanically robust due to its material properties. With its ultra thin profile, the cells can be constructed into several shapes in order to meet the specific requirements for its design. Furthermore, due to its robustness, DSSCs maintain their efficiency at high temperatures. The efficiency of the DSSC is between 10% and 11%, which is higher than other thin-film solar panels having an efficiency of only about 5% to 13% on average. DSSC technology also operates in low-light conditions (for example: cloudy weather where there is no direct sunlight), which is another reason why the DSSC is highly attractive among current choices for solar electrical generation. |
|
上一則
下一則
|
|
|
|
|
|
|
|
|
|